Is Laser Marking the Best Technology for Parts Marking?
Well, you might expect from a person with my background that there is only one possible answer. However, I believe that the appropriate answer is: It really depends.
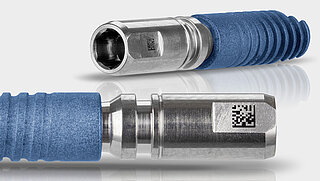
What are the advantages of laser marking?
Without any doubt, there are multiple benefits customers can reap with laser marking. Just to mention three of them, customers can…
- mark practically any content (e.g. text, 1D/2D codes, symbols) precisely, tamper-proof, reliably traceable and in many cases also with long durability,
- change between different marking contents very quickly, and
- carry out thousands and thousands of marks without worrying about any wear of tools or depletion of consumables.
And there are even applications, which you can only realize with laser marking, for example the delicate lacquer removal of symbols on buttons for cars. I mean those buttons, which you have in your car dashboard and which are so nicely back-lit with blue, white, red or any other light at night.
Are there any applications for which laser marking is not the first choice?
You recall that my answer above was “It really depends”. What I meant is that there are use cases where laser marking is not the best answer. You can group these cases in three categories:
- #1: Laser marking does not technically fulfil your application expectations.
- #2: Laser marking technically fulfils your application expectations but falls short on your production requirements.
- #3: Laser marking technically fulfils your marking and production expectations, but it does not pay off commercially.
Let me give you an example for each category:
- Ad #1: Let’s say your marketing colleagues approach you and demand that you need to find a way to mark the company logo on a moulded plastics part with a specific colour, for example red. Then you can immediately remove laser marking from the list. In such a case, it is worth thinking about pad printing or hot stamping.
- Ad #2: Your logistics colleague wants to print a lot of content in large size on the carton boxes which move on a conveyor through the packaging area. Well, you will often be able to laser mark carton boxes with the requested content and with sufficient contrast. But the showstopper here is that laser marking is typically way too slow for large size printing. A laser beam has a very small beam spot and therefore marking large characters would really challenge your patience. In this case, you could tell your logistics colleagues to take a closer look at large character printers or label applicators.
- Ad #3: The colleague from the workshop of your company needs to create a durable mark on just a few metal components per day. The mark is a simple serial number, which only needs to be human-readable. No contrast is needed and thus a simple engraving will be fully sufficient. Well, in such a situation you could use laser marking to achieve a very nice durable contrast mark on the metal components. But hey, the laser marking systems would for sure not rank first in terms of ROI. Here a micro-percussion or scribing units would be good.
What is the best technology for reliable industrial part marking?
As you have seen, there is a good reason for the diversity of marking technologies in the market. That is why there is no generally applicable answer to this question.
The bottom line:
- Laser marking is a great and useful marking technology.
- Yet, it is not the silver bullet, i.e. best choice for every marking application.
- For this reason, do not hesitate to ask the laser sales engineer of your trust straight-forward for his or her advice, whether laser marking makes technically and commercially sense for your specific marking and production task.